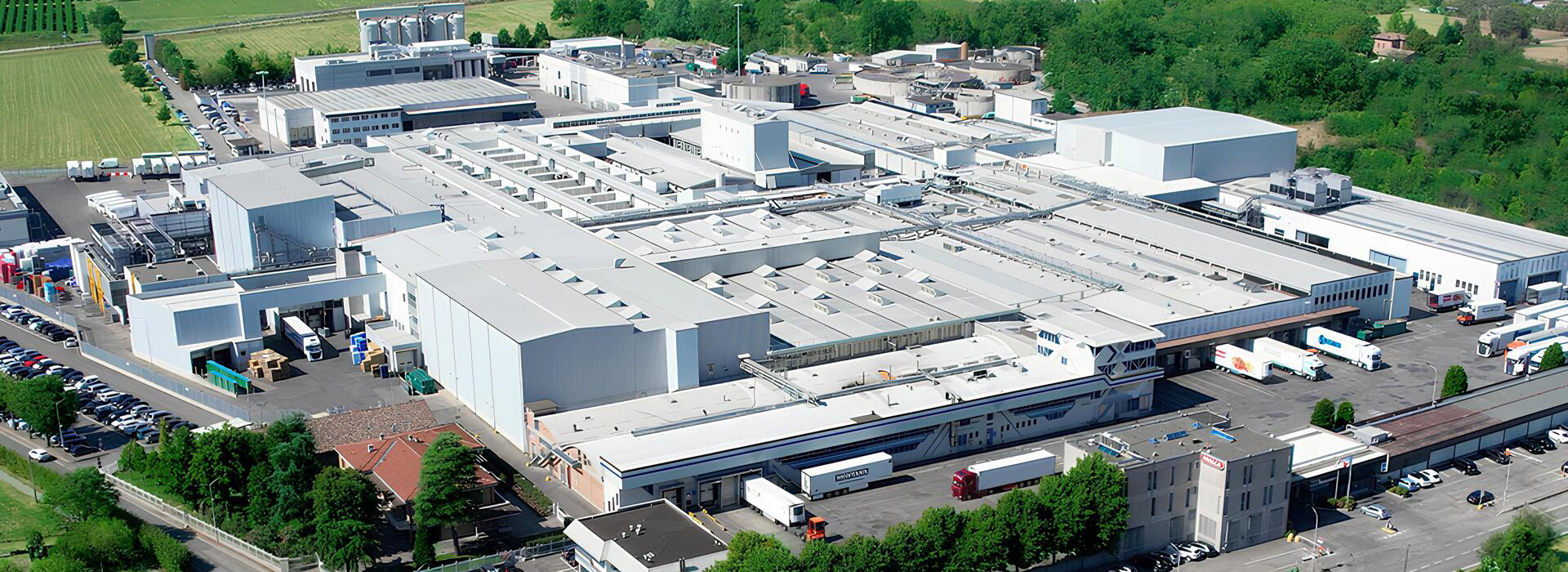
CASE STUDY
PSA Italy for Inalca
As part of our series on the companies that use the services of the PSA Italy terminals, we met Simon Neganti, Logistics Manager at Inalca, part of the Cremonini Group.
Inalca and the Cremonini Group
For sixty years the Cremonini Group has been a benchmark for the food industry at a national and international level. In 1963, Luigi Cremonini began his activity in the beef sector with the foundation of Inalca, which led to the creation of the modern meat industry. In the early 1970s, he began to diversify, initially expanding into the associated sector of cured meats and later in two complementary markets: in 1979 with the acquisition of MARR S.P.A he entered the food distribution sector and in 1982 he entered the catering business. Thus, the foundations of the group’s structure were laid down: production, distribution, catering.
How does one become a world player in such a competitive sector as that of food?
In Italy, Inalca has created an integrated production chain that goes from livestock farming to distribution. It was from precisely this last link, distribution, that the Group’s international activity began; a sort of backwards integrated production chain, in which the production and transformation phases take place at a later moment. In fact, today Inalca is permanently established in Russia and several African countries with logistic-distributive platforms and production structures. Inalca’s international activities now make up 50% of its turnover, and are based on a model that has led it to be the only company among leading beef producers on the world scene to be involved not only in production but also in the global distribution of raw materials, high quality foodstuffs Made in Italy, and more besides.
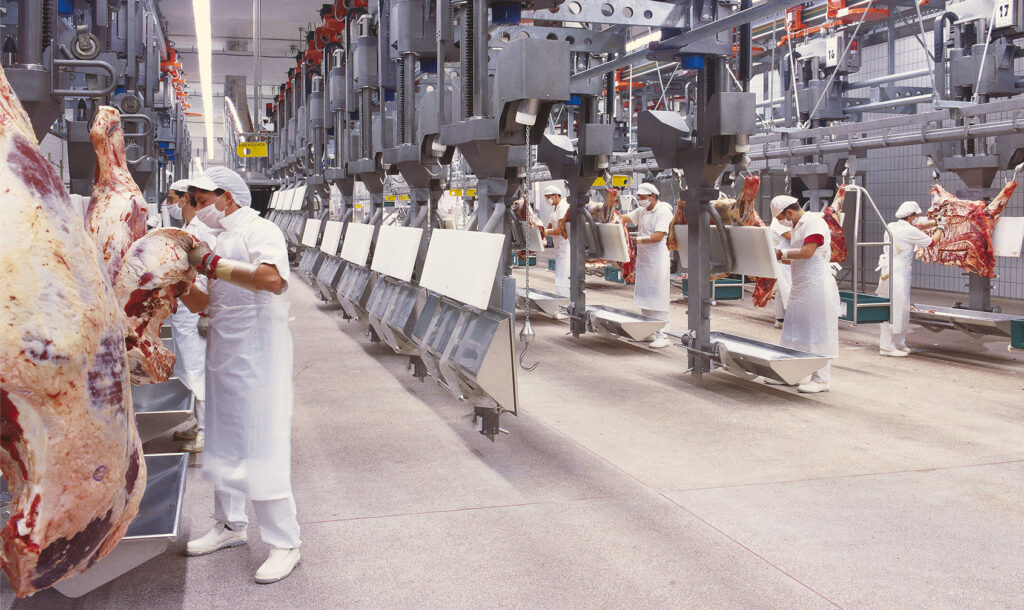
How many people are employed by Inalca?
Overall, the employment situation is substantially stable: 6,225 employees of which 4,219 at Inalca Group Italy and partners, and 2,006 employees at our overseas branches. In 2021, the Group increased the number of employees when it acquired new structures for pork processing in Italy.
How important to the company is the philosophy of food made in Italy, in terms of quality and quality control?
The founding principle of Inalca is based in the ancient traditions of Italian agriculture, which inspires and sustains the company’s development model. Inalca’s success derives from the ability to combine efficiency and economic results that guarantee growth and occupation along the entire production line, with a close connection to the territory in which the company operates. Activities that also contribute to the global challenge of producing food that is accessible and safe for all.
Which are your main export markets?
Inalca’s competitive model, which makes it unique on a global level, is based on the flexibility of its own production, which makes it possible to propose specific products for destination markets based on local request, thus optimizing the industrial processes and avoiding waste. Without doubt, Europe represents our main market. Other important markets are Russia, the African continent (we are present with over 15 distribution platforms) and emerging markets in Asia, in particular China, where we are the first Italian meat producers to have obtained an export license.
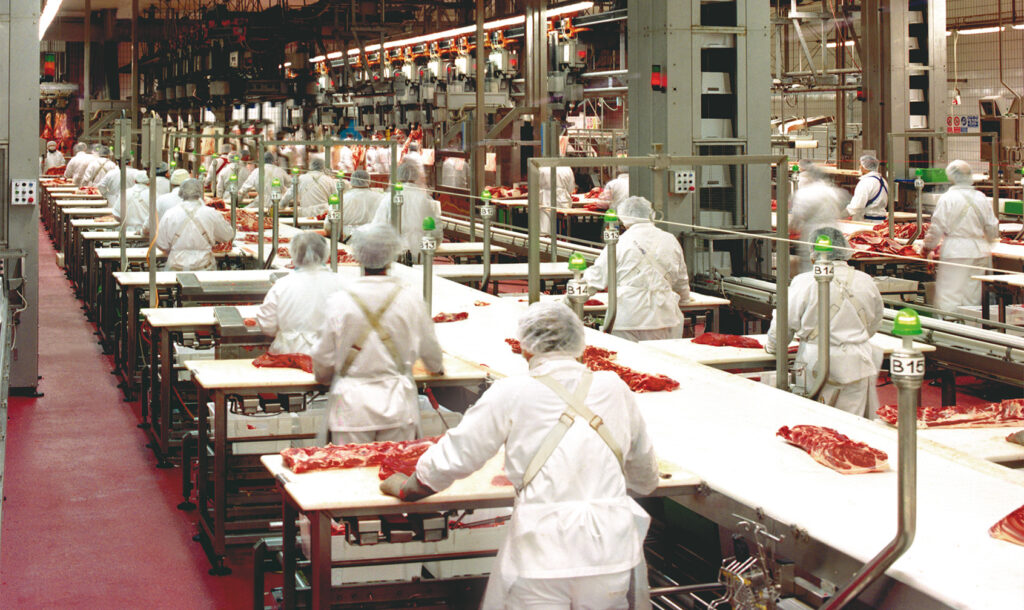
What percentage of the company’s turnover is made up of exports and what are the predictions for this year?
The external development of our activities has always characterised our business and our growth. Today, exports represent about 50% of our turnover. In these years of political-economic uncertainty, the data presents as stable.
World logistics is going through a period of great changes, which are revolutionising all sectors of industry. What are the main logistical challenges you face today?
We are faced with various challenges deriving from the great tensions characterising this historical period, both at global and national level. One of the main problems is finding vehicles and drivers who can guarantee a rapid and efficient service. Another matter of great impact is the rise in the cost of services caused by the increase in the price of raw materials. Last but not least, the commitment and work we dedicate to the theme of sustainability along the entire logistical chain, a central and strategic element for this company.
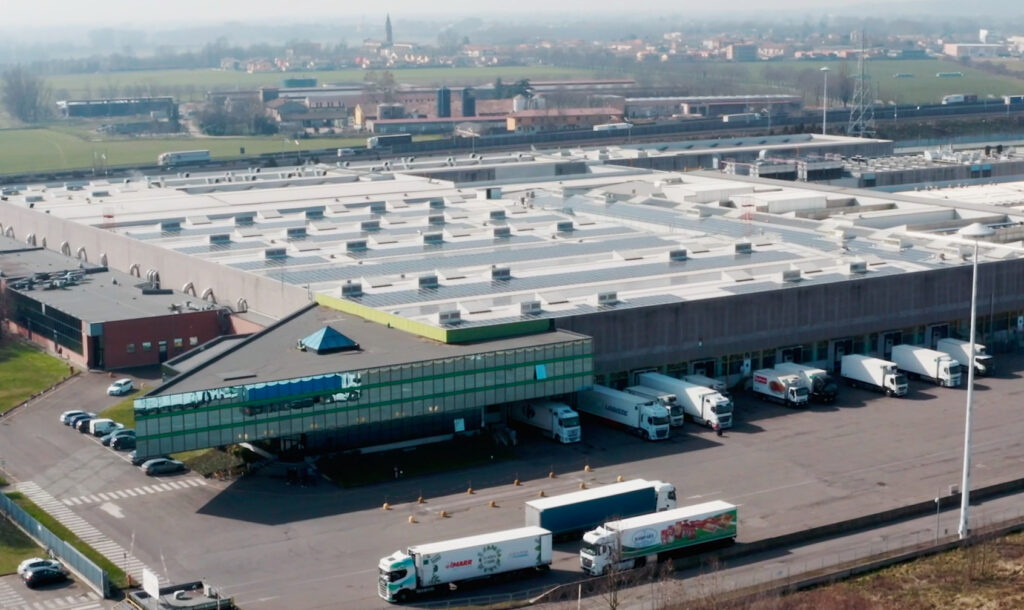
What are the keys to global logistical success for the food industry?
In the food industry the logistics must be fast and streamlined. The management services, both regarding transport and customs clearance must be the most efficient possible. Therefore, the key to success can be identified in the creation of a fast and efficient logistical chain, with specific services via land or sea and the shortest possible journey times.
What are the advantages to be gained from using the PSA Italy terminals for your import-export flow?
Using the PSA group terminals is advantageous for the quantity and variety of services offered, as it is a port of reference for the principal international routes. Moreover, the web portal available to customers, easy to consult and always updated, offers numerous functions and live monitoring activities that enhance the efficiency of the service.